Connected services & support
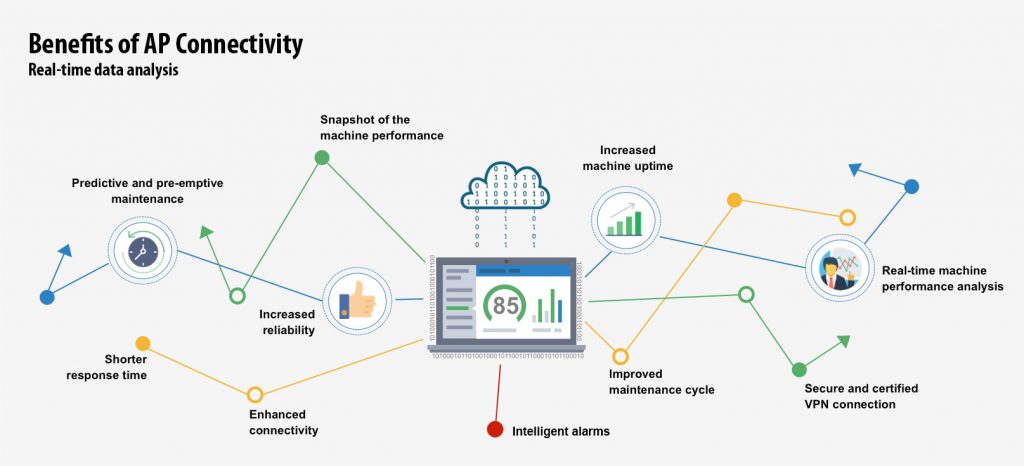
At Automationspartner we understand how important it is for you to be able to rely on your machine equipment for top performance and professional service to ensure that downtime is kept to a minimum.
Data-driven decision making will dramatically alter the way your organization works with scheduled service. Rather than focusing on corrective service, a data-driven monitoring system can be programmed to automatically request support from an internal or external service team when parameters deviate or fluctuate from a set value or range.
To efficiently work with a self-monitoring machine it is important to have a strategy and to fully understand what functions are paramount and more necessary to monitor than others. To get the most out of the system you need qualitative data rather than quantitative.
Our automation engineers will normally begin by mapping the various stations and their cycle times as the first level of data analytics. Being comfortable with the data management, the second level of data from individual cylinders, motors, valves etc can be applied. You might want to totally avoid a cylinder malfunction by letting the monitoring system send out a request for a part replacement when reaching 80% of its theoretical lifetime. In this way, a part replacement can be scheduled during a batch shift and managed in a couple of minutes rather than causing a machine stop and a loss of profit.