Supporting customers is a top priority for any company. The ever-going globalization and relocation of productions sites might put your company and service team in a situation where you traditionally would be well prepared but suddenly find yourself with a challenging task at hand – to support your machines at remote locations.
You will need to develop methods that both are safe and efficient.
An automated assembly line that malfunctions or do not operate is costly and will therefore always require urgent support. In the MedTech industry, a machine stop can easily cost the production line owner tens of thousands of dollars per day.
Besides the urgency for support mentioned above, there are a lot of technical aspects that need to be taken into consideration when working remotely on live production lines. What happens if a power failure or surge occurs while updating the system remotely? How do you evaluate the update and perform a safe backup?
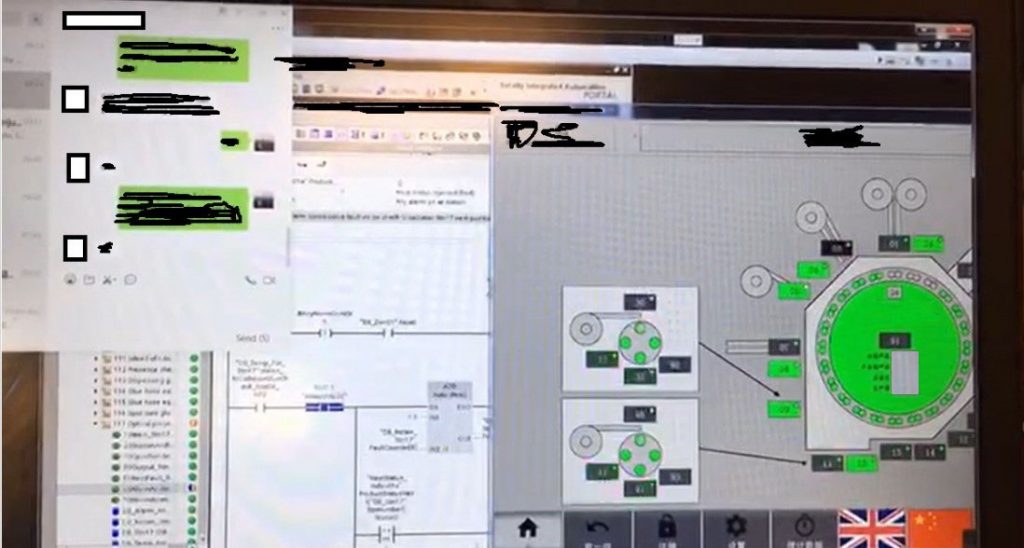
Is it also possible to work efficiently with predictive maintenance remotely?
Of course. The foundation of predictive maintenance is to work with and focus on relevant data. The data is processed on a “Fog”-level for later evaluation in the Cloud.
To see how this data can generate machine uptime we use a single cylinder as a simple example.
When the cylinder is working normal, it has a cycle time of Y(s), i. e. the time it takes to perform one full cycle moving its piston from a to b and back to a. After X strokes, internal parts and components will start to wear out and that will in most cases affect the cylinders cycle time.
By analyzing the cycle time, we can identify a deviation from its nominal speed. When the deviation is outside a set range the monitoring system can trigger an alarm.
It is also possible to enter the cylinders theoretical lifetime as data into the system. Continuously counting cylinder strokes, the system will alert the service department when closing in on the expected time to failure. In this way, the service department can order and replace the unit at a scheduled service stop rather than letting it cause machine failure.
Subsequently, you can also create an algorithm that sets a relation between the expected time to failure and actual performance deterioration. In this way, the system “learns” when it would be reasonable to start thinking of replacing the cylinder. You do not want to replace a fully functioning unit.
By working smarter with data, unwanted downtime and spare parts inventory can be reduced to a minimum.
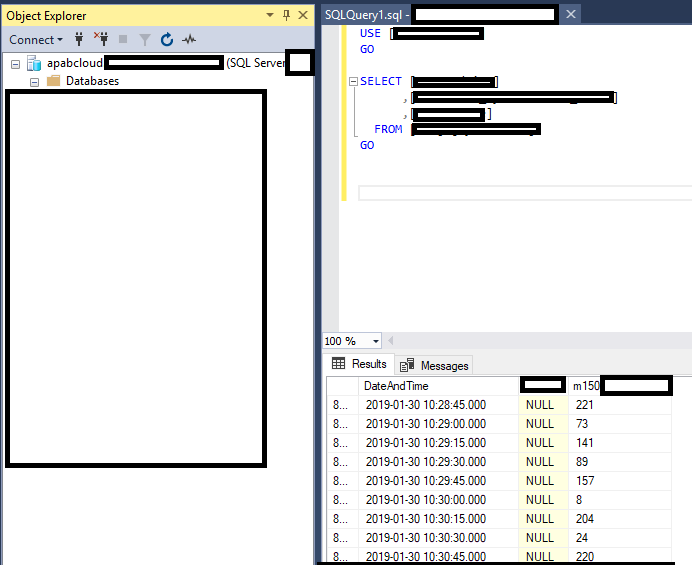
Choosing Microsoft Azure as a foundation for the cloud, it does not matter if your machine is in South-east Asia or America. The Azure datacentres are in 54 locations worldwide and available in over 140 countries providing a safe and reliable SQL server.
Contact us If you want to know more about how we at Automationspartner work with data monitoring in our automated MedTech production lines for optimization and remote support.
For technical questions please contact:
Victor Ottosson – Automation Engineer
For commercial questions and how you can work together with AP please contact: